Comprehensive Guide to PV Cable Testing Procedures
Introduction
Photovoltaic (PV) systems are becoming increasingly popular as a sustainable and renewable energy source. These systems rely on various components, including PV cables, to safely and efficiently generate electricity from sunlight. Proper testing of PV cables is crucial to ensure the reliability and longevity of the entire PV system. In this comprehensive guide, we will delve into the importance of PV cable testing procedures, the different types of tests that can be conducted, and the step-by-step process for conducting these tests.
Importance of PV Cable Testing
PV cables play a critical role in the overall performance of a PV system. They are responsible for transmitting the generated electricity from the solar panels to the inverter and ultimately to the electrical grid or storage system. Faulty or degraded PV cables can lead to reduced energy output, safety hazards, and system downtime. Therefore, regular testing of PV cables is essential to identify any potential issues and ensure optimal system performance.
Types of PV Cable Tests
There are several types of tests that can be performed on PV cables to assess their quality and integrity. These tests help determine the overall condition of the cables and identify any defects or faults that may compromise their performance. Some of the most common types of PV cable tests include:
1. Insulation Resistance Test: This test measures the resistance of the insulation material surrounding the conductors. It helps identify any moisture ingress, physical damage, or deterioration of the insulation that could lead to electrical faults.
2. Continuity Test: The continuity test checks for a continuous path for electrical current flow along the length of the cable. It ensures that there are no breaks or open circuits in the conductors that could impede the flow of electricity.
3. Voltage-Withstand Test: Also known as the dielectric strength test, this test assesses the ability of the cable insulation to withstand high voltages without breaking down. It helps determine the insulation integrity and the overall safety of the cable.
4. Temperature Rise Test: This test evaluates the thermal performance of the cable under load conditions. It assesses the cable's ability to dissipate heat and maintain safe operating temperatures during normal operation.
5. Flame Propagation Test: This test measures the cable's resistance to flame propagation and fire resistance. It is crucial for ensuring the safety of the PV system in the event of a fire.
6. UV Resistance Test: Exposure to sunlight can cause degradation of the cable insulation over time. The UV resistance test evaluates the cable's ability to withstand UV radiation and maintain its performance and longevity.
7. Mechanical Stress Test: This test assesses the cable's resistance to mechanical stress, such as bending, twisting, and pulling. It ensures that the cable can withstand the rigors of installation and operation without damage.
Step-by-Step PV Cable Testing Procedures
Now that we have discussed the importance of PV cable testing and the different types of tests that can be conducted, let's explore the step-by-step process for performing these tests:
1. Preparation: Before conducting any tests, ensure that the PV system is safely shut down and de-energized to prevent any electrical hazards. Gather all the necessary testing equipment, including a multimeter, insulation resistance tester, continuity tester, and any other specialized tools required for specific tests.
2. Visual Inspection: Start by visually inspecting the PV cables for any signs of damage, wear, or degradation. Look for cracks, cuts, abrasions, or discoloration on the cable insulation. Check for loose connections, exposed conductors, or any other visible defects that may indicate potential issues.
3. Insulation Resistance Test:
a. Disconnect the PV cables from the system to isolate them for testing.
b. Use an insulation resistance tester to measure the resistance between the conductors and the cable insulation.
c. Compare the measured resistance values against the manufacturer's specifications to determine the insulation integrity.
4. Continuity Test:
a. Use a continuity tester to check for a continuous path for current flow along the length of the cable.
b. Connect the tester probes to each end of the cable and verify that there is no break or open circuit in the conductors.
c. Ensure that the resistance reading is within the acceptable range to confirm continuity.
5. Voltage-Withstand Test:
a. This test should be conducted by a qualified technician using specialized equipment designed for high-voltage testing.
b. Apply a high voltage between the conductors and the cable insulation for a specified duration to assess the dielectric strength.
c. Monitor for any breakdown or flashover and ensure that the cable insulation can withstand the test voltage without failing.
6. Temperature Rise Test:
a. Apply a known load to the cable and monitor the temperature rise over a specified period.
b. Measure the temperature at various points along the cable length and compare it against the allowable temperature limits.
c. Ensure that the cable can dissipate heat effectively and maintain safe operating temperatures under load conditions.
7. Flame Propagation Test:
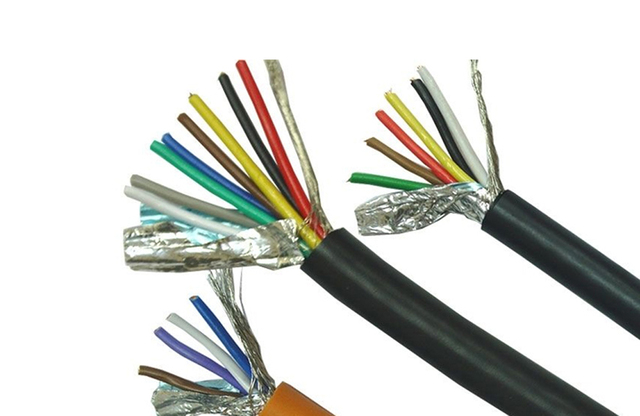
a. Conduct the test in a controlled environment using a standardized flame propagation test apparatus.
b. Expose the cable sample to a flame source and observe the flame spread along the cable length.
c. Assess the cable's resistance to flame propagation and its ability to self-extinguish after the flame source is removed.
8. UV Resistance Test:
a. Expose the cable sample to UV radiation for a specified duration using a UV chamber or natural sunlight.
b. Monitor the cable insulation for any signs of degradation, such as discoloration, embrittlement, or cracking.
c. Evaluate the cable's ability to withstand UV exposure and maintain its performance over time.
9. Mechanical Stress Test:
a. Apply mechanical stress to the cable sample by bending, twisting, or pulling it to simulate installation and operation conditions.
b. Check for Mineral insulated cable lifespan , deformation, or insulation breaches that may occur under stress.
c. Verify that the cable can withstand mechanical stress without compromising its electrical integrity.
10. Documentation and Reporting:
a. Record all test results, including measurements, observations, and any deviations from the expected values.
b. Prepare a comprehensive test report detailing the procedures followed, equipment used, test results, and recommendations for any corrective actions.
c. Maintain detailed records of all PV cable tests for future reference and compliance with regulatory requirements.
Conclusion
In conclusion, proper testing of PV cables is essential to ensure the safety, reliability, and performance of a PV system. By following the comprehensive guide to PV cable testing procedures outlined in this article, system owners, installers, and maintenance personnel can effectively assess the quality and integrity of PV cables and address any issues proactively. Regular testing and maintenance of PV cables will help maximize the efficiency and longevity of the entire PV system, ultimately contributing to the success of renewable energy initiatives worldwide.